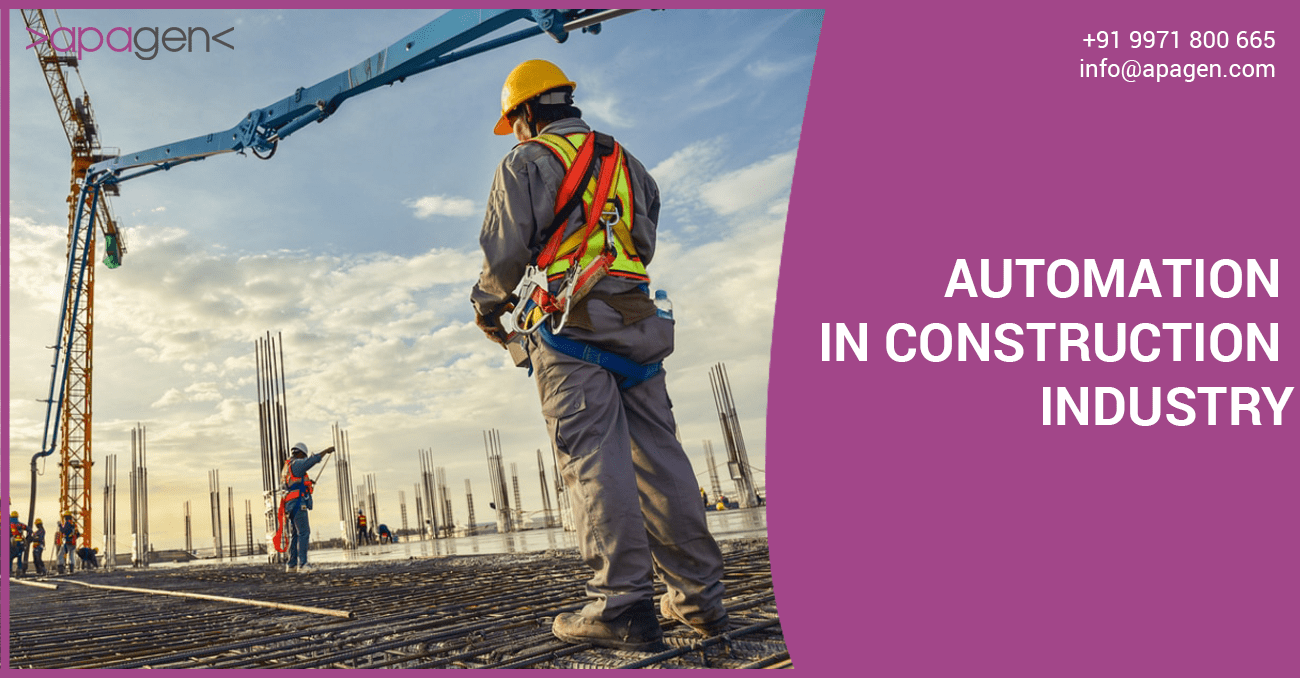
The impact of Automation in Construction Industry
While the phrase “automation” could conjure pictures of robots taking up jobs, the fact is far more nuanced. In construction, for example, automation is much less likely to diminish employment alternatives than it’s to extend productivity. Indeed, automation in the construction industry—alongside the worldwide need for brand-new and up-to-date infrastructure and better and more inexpensive housing—may help shape the direction of the business. The key can be anticipating and getting ready for the shift, partially by growing new skills within the present and future workforce.
In years previous, productiveness in construction elevated slowly at best. In the United States, as an illustration, from 1947 to 2010, productiveness in construction was barely modified in any respect. Meanwhile, productiveness is elevated by greater than an element of eight in manufacturing and by greater than an element of 16 in agriculture —each industry that has embraced automation. So, one main advantage of automation in the construction industry is the potential for fairly a big uptick in productivity.
There are three main opportunities for automation in the construction industry. The first is automation in the construction industry of what is thought of as traditional physical duties on-site—for example, robots laying bricks and machines paving roads. The second opportunity comes from the automation of the modular construction industry—or quite a production—in factories, together with 3-D printing of elements similar to facades. And the third facilities on digitization and the following automation of design, planning, and administration procedures, in addition to the huge efficiencies these can create on-site. For instance, constructing data modelling—which basically brings collectively the designs of planners and common contractors to determine issues earlier than they move to the location—makes the planning process more efficient. But more importantly, it makes the on-site execution extra efficient, permitting project groups to remove errors and higher coordinate the workforce.
What impact will Automation in construction industry have on work for builders?
A substantial shift to modular construction off-site could have a major impact on the construction workforce, however, the transition will take many years. Producing particular person elements, or modules, in factories lends itself to far more machine use than what could be completed on-site. Some corporations are already constructing such modules. A whole lot of the development in these factories remains to be completed manually, however over time, as scale will increase, the method will become more automated. We estimate that about 15 to 20 % of the latest construction building can be modular within the United States and Europe by 2030. So, whereas it’s a rising share and a giant market, it’s a sluggish process, and a variety of actions will stay on-site and comparatively unpredictable for a while to come.
For these actions that do stay on-site, it’s unlikely that an organization will fireplace a carpenter and convey within the newest robotic to do every little thing the carpenter did. Rather, machines will take over particular person actions inside a task. What which means is employees might want to study to work facet by facet—or in a hybrid position—with machines. For instance, even the common construction employee can be anticipated to use a pill to access building plans or function a drone instead of doing a bodily website walkthrough.
Will there be sufficient work sooner or later?
While there are substantial automation alternatives throughout industries, employment in construction will probably undergo lower than in industries where activities are more repetitive, similar to manufacturing. The best tasks to automate are repetitive, physical activities in predictable environments—however, development’s environment is often unpredictable, except when modular-construction methods are used. The unpredictability is twofold: not only do items transfer around however every construction site and the project is tailor-made to particular customer demands, architectural designs, and geographical and site necessities.
We anticipate the overall variety of jobs in construction to develop rather than shrink, with as much as 200 million extra jobs by 2030 if nations fill international infrastructure gaps and increase affordable housing supply. Automating more of the development process might additionally assist deliver infrastructure and buildings faster—without having to scale back headcount. Furthermore, there’s a substantial need for infrastructure and housing in components of Asia and Africa. This means there can be demand for construction industry work—and workers—for a very long time to return.
Any slowdown in international development, which might decrease demand for infrastructure investment, may counter a few of that upside. But, usually, there’s—and we anticipate there to proceed to be—sufficient work to do.
How will automation have an effect on construction wages?
Despite everyone having enough work to do, we anticipate a bigger spread in wages. In the long run, automation is likely to improve productiveness and permit wages to rise for employees with advanced expertise. At least through the transition time—which might take a decade or longer—these with superior skills will command larger wages because they will be in larger demand, while these extra uncovered to predictable, repetitive duties can be in much less demand and might even see a slowdown of their wage development.
Overall, building jobs are usually within the middle-wage vary, at least within the United States, and aren’t easy to automate. Therefore, the business may contribute to filling in what in any other case seems more likely to be a continued hollowing out of the center class.
How can the business handle the upcoming workforce expertise transition?
As in all industries, automation will create a growing skill mismatch in construction. Workers will still want a good amount of physical expertise: even when robots do the physical work of laying bricks, employees will still have to drive and manoeuvre heavy equipment. But they might want to pair this work with more technological expertise.
But the place will they purchase these skills? Adjusting to automation in construction would require efforts from the public sector, the personal sector, and business associations to help workers in growing the abilities to make the transition.
Historically, the public sector has had a predominant role in supplying baseline training and expertise, and it’ll probably proceed to take action. But curricula should shift to satisfy present and future needs, notably for technological and socioemotional expertise. There may even be a rising have to reskill and upskill employees who left formal education many years in the past, requiring an evolution of the training system to supply lifelong studying alternatives.
The personal sector, in the meantime, has accountability to address the extra specialised abilities wants of the workforce—and throughout sectors, a majority of executives acknowledge they’ve a powerful position to play. But traditionally, construction has invested a lot lower than different industries do in staff’ expertise. This is partially a result of the predominance of subcontractors and excessive shares of momentary labor. But as all companies face the identical expertise shift, it would turn into more and more troublesome to seek out certified individuals in the marketplace. Institutions should preempt the necessity and supply access to skill-development alternatives, investing in their present workforce so they’re ready for the job forward.
No Comments